Výrobní areál na severu Čech Jungheinrich AG v současnosti produkuje vlajkovou loď koncernu, retrak ETV 216i. Jeho výroba se sem stěhuje z německého Norderstedtu. Uvolněná kapacita v Německu bude využita k rozšíření jeho výrobního portfolia o náhradní díly pro další vychystávací vozíky.
Během slavnostního otevření závodu zástupci společnosti vůbec poprvé informovali o tom, že kromě typu ETV 216i se u Chomutova začnou vyrábět také další řady vozíků s výsuvným sloupem, například ETV c16/c20. Poprvé také předvedli prototyp nástupce ETV 216i, který má nyní interní označení NGS. Bližší podrobnosti o jeho technických parametrech dosud nebyly zveřejněny, z dostupných informací vyplývá, že přinese změny evolučního charakteru.
Při projektování nového závodu v Chomutově kladla společnost Jungheinrich zvláštní důraz na efektivitu a udržitelnost. Celý závod, od pracovišť až po komplexní výrobní zařízení, využívá nejmodernější technologie. Kromě plně automatizovaného centra pro detailní zpracování kovů je například vybaven inovativní lakovací linkou, která současně spotřebovává méně energie i materiálu pro vysoce kvalitní práškové lakování. Výroba a montáž s digitálním asistenčním systémem mají za cíl zajistit efektivitu a kvalitu procesů. Toho se mimo jiné dosahuje využitím umělé inteligence.
Pozvaní hosté měli počátkem října možnost prohlédnout si v podstatě celý výrobní proces. Stožár bočně vedených vozíků ETV 216i se skládá ze tří profilů, které na začátku opracuje automatická fréza. Tyto díly pak zamíří do svařovacího robota, z něhož vyjde stožár v surovém stavu (je nutné jej poté ještě očistit a vyrovnat).
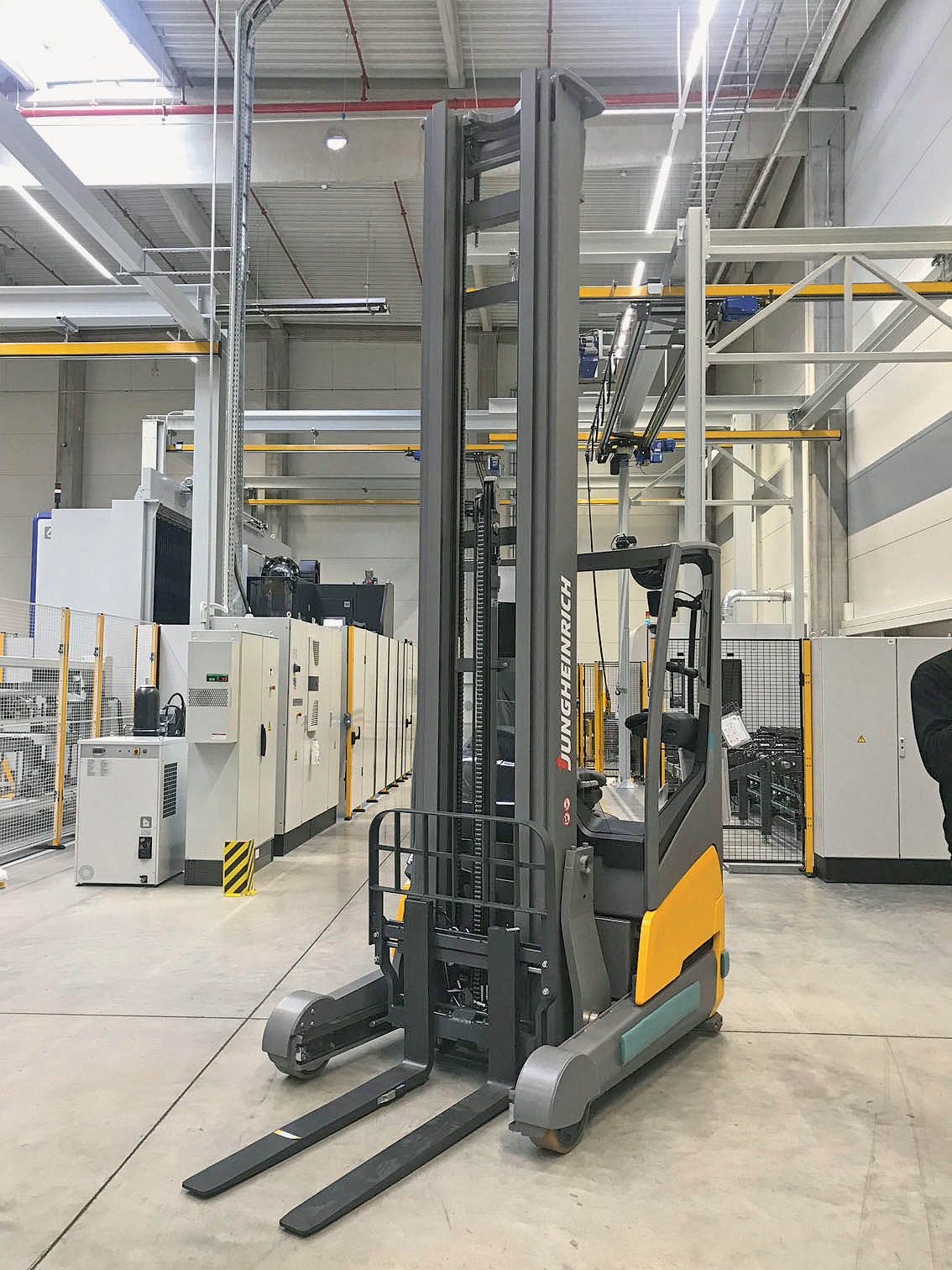
Na sousedním pracovišti se vyrábí podvozek, principiálně velmi podobně jako u osobního auta. Držák stožáru se dosud vyrábí v Norderstedtu, v budoucnu se jeho výroba přesune také k Chomutovu.
Všechny obráběcí a řezací procesy probíhají za sucha, aby na všechny díly stoprocentně přilnula barva. V lakovně se navěšuje podvozek, držák stožáru, i stožár samotný, proces probíhá plně automaticky, manuálně se barva nanáší pouze do různých strojově nepřístupných záhybů. Komponenty potom míří do pece na vypečení, poté do chladicí komory a po vychladnutí jsou připraveny na finální montáž.
K podvozku se na linkách přidá kabina (dodávaná externím dodavatelem) a hotový stožár. Předtím ještě do kabiny a na kabinu operátor montuje různé další komponenty, jako jsou sedačky, volanty, zrcátka nebo světla. Při finálním zpracování je na podvozek rovněž dodáváno protizávaží, celý vozík je oživen nahráním řídicího softwaru.
Stroje se podle přání zákazníka doupravují různými inteligentními senzory, couvacími kamerami, výstražným osvětlením a podobně. Vlastnosti všech vyrobených vozíků se prověřují v zátěžovém provozu ve speciální testovací věži, kvalita laku je potvrzena ve světelném tunelu.
Zaujal vás článek? Pošlete odkaz svým přátelům!
Tento článek je odemčený. Na tomto místě můžete odemykat zamčené články přátelům, když si pořídíte předplatné.